Ford Focus mk3 charging system description
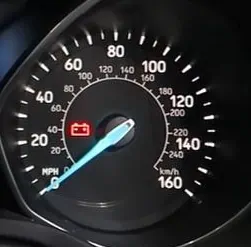
Overviev
The generator is driven by the FEAD belt. When the engine is started, the generator begins to generate AC, which is internally converted to DC. The DC is controlled by the voltage regulator and supplied to the battery. The PCM controls the voltage regulation setpoint, communicating with the generator internal voltage regulator over a dedicated LIN communication circuit.
CHARGING SYSTEM - SYSTEM OPERATION AND COMPONENT DESCRIPTION
The smart regenerative charge system primary strategy is stored in the BCM. The BCM receives all of the important information relating to the battery condition from the battery monitoring sensor via the LIN. The BCM calculates and sends the set value needed for the generator charging voltage via the High Speed Controller Area Network (HS-CAN) to the PCM. The PCM then adjusts the value received (if necessary) and sends it to the generator via the LIN. The charging voltage is adjusted depending on various parameters, such as the current level of engine efficiency. The smallest possible set value for the generator voltage is 12.2 volts, while the maximum charging voltage can be anywhere between 14.5 and 14.9 volts. However, when the battery is in a refresh phase, the voltage may occasionally reach up to 15.2 volts. These refresh phases are required when the battery charge status is 80% over long periods of time, which increases the risk of sulfation in the battery cells.
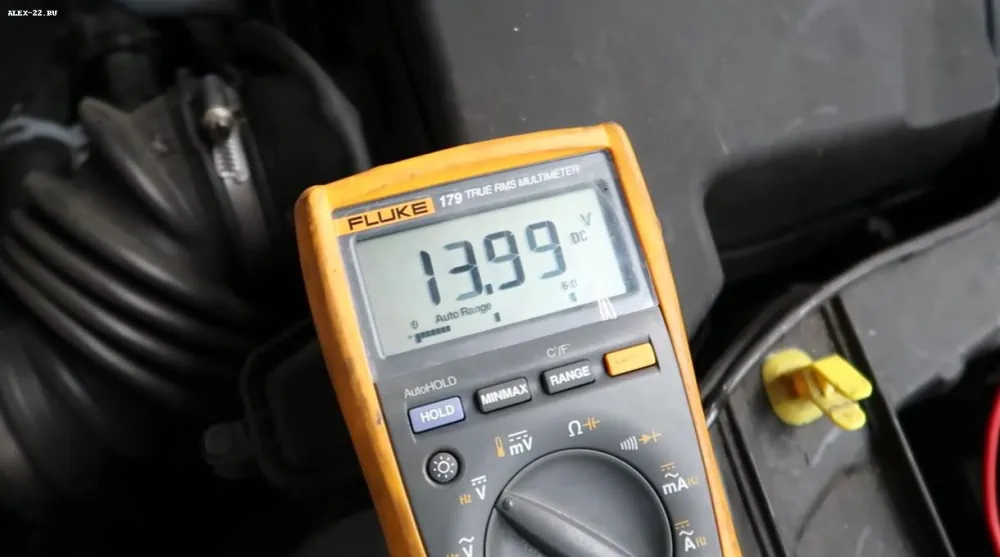
The PCM simultaneously controls and monitors the output of the generator. When the current consumption is high or the battery is discharged, the PCM raises engine speed as needed to increase generator output. The generator charges the battery and at the same time supplies power for all of the electrical loads that are required. The battery is more effectively charged with a higher voltage when the battery is cold and a lower voltage when the battery is warm.
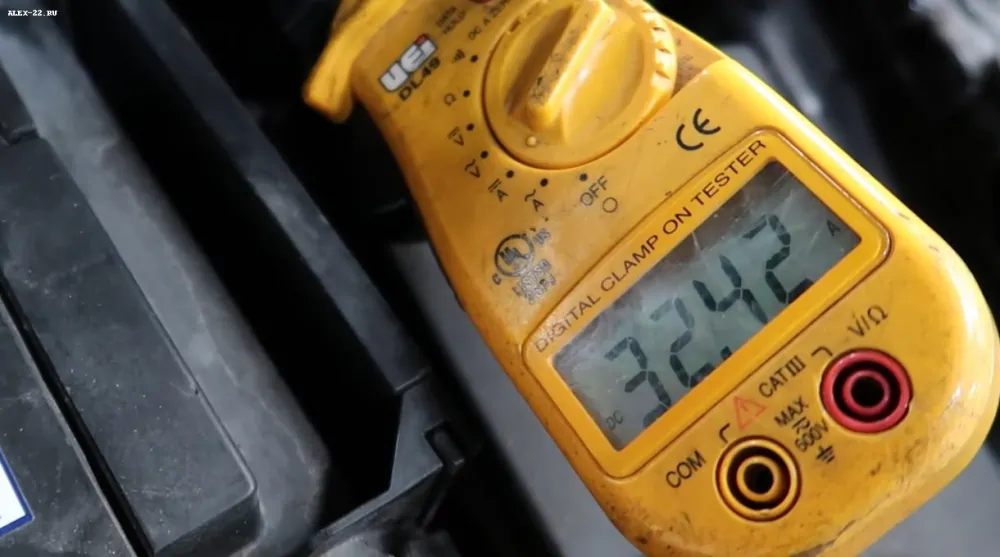
The PCM turns off the generator during cranking to reduce the generator load and improve cranking speed. Once the engine starts, the PCM slowly increases generator output to the desired voltage.
The PCM reports any charging system faults and sends a message through the High Speed Controller Area Network (HS-CAN) to the BCM. The BCM then sends a message over the Medium Speed Controller Area Network (MS-CAN) to the IPC, which controls the charging system warning indicator. The status of the PCM charging system warning indicator message can be confirmed by viewing the PCM Generator Fault Indicator Lamp (GENFIL) Parameter Identification (PID). Any charging system fault detected by the PCM results in 1 or more Diagnostic Trouble Codes (DTCs) being set and the GENFIL Parameter Identification (PID) having a status of ON. If equipped with a charging system warning indicator, the IPC turns the indicator on or off. If equipped with a message center, the IPC displays the corresponding message to notify the driver of the condition.
Under certain circumstances, the charging system may have a concern but still keeps the battery charged while the vehicle is running. The LIN is normally used to initiate charging, but the generator can charge with a fault in this circuit. If the engine operates at more than 2, 000 Revolutions Per Minute (RPM) momentarily, the generator self-excites or begins charging on its own. The charging system warning indicator is then illuminated and/or the corresponding message to notify the driver of the condition is displayed and the generator operates in a default mode (approximately 13.5 volts) until the engine is turned off. When the engine is restarted and the engine operates at more than 2, 000 Revolutions Per Minute (RPM) momentarily, the generator again self-excites and again the charging system warning indicator is illuminated and/or the corresponding message to notify the driver of the condition is displayed. The Smart Regenerative Charge charging system is designed to set 1 of 7 Diagnostic Trouble Codes (DTCs) any time a charging system fault is present. All of the Diagnostic Trouble Codes (DTCs) can set as continuous faults, but not all Diagnostic Trouble Codes (DTCs) set as on-demand faults.
BATTERY MONITORING SYSTEM
This vehicle is equipped with a Battery Monitoring System which manages battery charging by the generator and monitors the battery state of charge. The Battery Monitoring System also utilizes a load shed strategy to help control discharge of the battery and prevent, when possible, an excessively low battery state of charge. The BCM monitors the battery state of charge using the battery monitoring sensor attached to the negative battery terminal and cable assembly.
To maintain correct operation of the load shed system, any electrical devices or equipment must be grounded to the chassis ground and not the negative battery terminal. A connection to the negative battery terminal causes an inaccurate measurement of the battery state of charge and incorrect load shed system operation due to the current being used bypassing the battery monitoring sensor.
The battery monitoring sensor has to be recalibrated at regular intervals. This occurs during a rest period or when the battery closed-circuit current is less than 100mA. The rest period must last for at least 3 hours. The timeframe in which a recalibration must take place is 7 days. If the system has been unable to carry out a recalibration within this time then it is impossible to confirm the exact state of charge of the battery. Any devices left attached to the power socket that draw in excess of 100mA (or less depending on other battery loads) will prevent a battery monitoring sensor recalibration.
When the ignition is in ACC or ON mode and the BCM determines the battery voltage or the battery state of charge has dropped below set levels, a low battery warning message is displayed in the message center as described below. Should the battery voltage or the battery state of charge continue to drop, the audio system is powered down to save the remaining battery charge. This load shed state clears once the vehicle has been started and battery state of charge is allowed to recover.
When the ignition is in the ON mode and if load shed occurs, the message center can display the corresponding message to notify the driver that battery protection actions are active. The audio system shuts down after the message center displays the warning.
If a fault occurs with the battery monitoring sensor or circuit(s), the only engine off load shed strategy that is active is a 45 minute timer. After 45 minutes have elapsed, the audio system turns off. To clear the load shed state, restart the engine.
If the vehicle battery is replaced, carry out the Battery Monitoring System Reset using the scan tool. If the Battery Monitoring System Reset is not carried out, measurement data collected for the old battery will not be deleted and future state of charge measurements will be inaccurate. For example, if an old battery has a state of charge of 60% and the new battery has a state of charge of 90%, the BCM will recognize battery state of charge being 30% lower than it actually is. With the battery state of charge being perceived lower than it actually is causes shedding of loads earlier than is necessary. This also impacts the smart regenerative charge system by causing the battery to be maintained at a higher state of charge than perceived by the BCM, reducing fuel economy benefits.
If the vehicle has been jump started, test the battery condition.
BATTERY MONITORING SENSOR
The battery monitoring sensor is attached to the negative battery terminal and cable assembly, which provides a ground to the sensor. The battery monitoring sensor measures voltage, current and temperature of the battery and uses these inputs to calculate the battery condition, transmitting this information through the LIN circuit to the BCM. The battery monitoring sensor has a 2-pin connector providing battery voltage and LIN connections. The battery monitoring sensor has to be recalibrated at regular intervals. This occurs during a rest period or when the battery closed-circuit current is less than 100mA. The rest period must last for at least 3 hours. The timeframe in which a recalibration must take place is 7 days. If the system has been unable to carry out a recalibration within this time then it is impossible to confirm the exact state of charge of the battery. Any devices left attached to the power socket that draw in excess of 100mA (or less depending on other battery loads) will prevent a battery monitoring sensor recalibration.